Designations and structure. The system is designed for automatic tracking for a joint center with V-groove in gas-shielded welding of longitudinal (technological) pipe welds. The joint center is a point corresponding to groove root in transverse direction and averaged coordinate of groove edges on vertical line.
The system consists of two elements, namely laser sensor and communication module. The laser sensor is designed for contact-free measurement of transverse and longitudinal displacement of the joint center. Also the sensor is used for measurement of additional parameters such as joint width, edge displacement and groove angle. The main functions of the communication module are data receiving from laser sensor, formation of signals of vertical and transverse correction of welding head position, visual monitoring of operation and adjustment of the tracking system using LCD display equipped with sensor screen, interaction with the main controller of the welding mill and external computer during system parameterization. It is also possible to connect the external display via VGA interface.
The tracking system is imbedded in existing process equipment of welding mill using a series of external interfaces, i.e. discrete and analogue inputs/outputs, serial interface RS-232/485, Ethernet and another (on Customer demand).
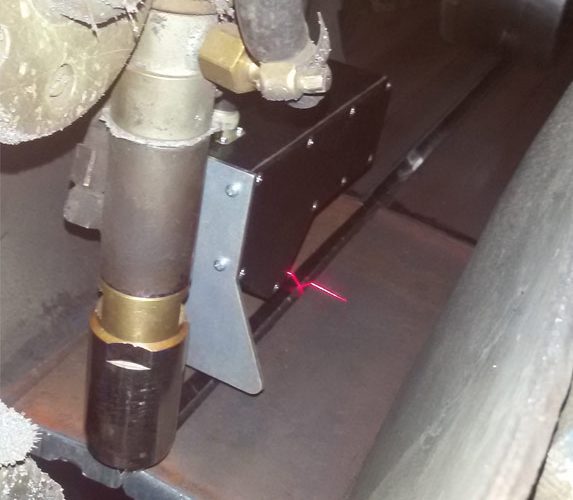
Main advantages of STS-200-SBS tracking system (in comparison with close analogues)
- high sensitivity to groove depth due to large triangulation angle and high resolution ability of photoreceivers of the laser sensors that provides reliable joint tracking in welding of parts with small groove;
- unique optical path and special algorithm for video signal processing eliminate effect of re-reflection in the groove and optical radiation of welding arc on joint tracking process;
- reliable algorithm for protection of system “deviation” in the case of mechanical interferences in the joint zone;
- on-line TV signal that allows visual monitoring of tracking process for welder;
- quick performance recover – time of full reboot of the system does not exceed 5 seconds;
- transformer galvanic isolation of power supply and signal circuits is realized directly in the laser sensor that eliminate effect of electromagnetic interferences of welding cables;
- replaceable laser sensors and communication modules cut expenses for spare parts;
- simple maintainable cables;
- protection glasses of standard 20 and 30 mm diameter can be easily replaced for several minutes.
Performance characteristics
Accuracy of joint center tracking in transverse and vertical directions, mm | ±0,5 |
Accuracy of measurement of joint edge exceeding, mm | ±0,2 |
Maximum operating area of sensor in transverse direction, mm | ±30 |
Maximum operating area of sensor in vertical direction, mm | ±25 |
Nominal distance from sensor to pipe, mm | 40 |
Minimum allowable groove depth, mm | 3 |
Maximum length of communication line between sensor and communication module, m | 50 |
Connection of external display | VGA, 1024´768 px |
Power supply | ~220 В |
Consumed power, W, not more | 30 |
Breakdown voltage of sensor galvanic insulation, kW, not less | 1,5 |
Sensor IP protection | IP64 |
Range of operating temperatures of sensor, °С | -10..+65 |